Electropoli
European leader in surface treatment
We have been developing a wide range of strategic research areas for more than 70 years, which today enable us to support you in every aspect of your project.
Drawing on our extensive surface treatment expertise, we undertake to provide you with advice and deliver solutions that not only meet your specifications but also include any related requirements you may have (logistics, quality, environment, packaging, etc.)
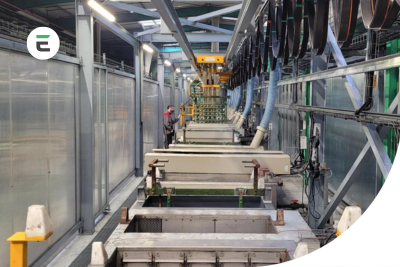
Electropoli reinforces its Zinc-Nickel production capacity!
In the context of REACH regulations, the aeronautics, defense and space (ADS) sectors are accelerating their transition to more environmentally-friendly technologies.
At Electropoli, we are supporting this development by increasing our production capacity, with the support of major customers and thanks to the qualifications obtained in recent years.
Our Isigny-le-Buat site is now equipped with four Zinc-Nickel treatment lines, complementing our certified processes: Surtec 650, electroless nickel and liquid paint.
A further step towards guaranteeing our customers a secure supply, in line with the most stringent market requirements!
On February 20, 2025, Nicolas DELAHEGUE, President & CEO of the Electropoli Group, was invited to attend the Economic and Commercial Exchange and Innovation Cooperation Meeting between Changzhou and Shanghai, organized as part of New Year's Week. Held along the banks of the Huangpu River in Shanghai, this event brought together over 200 key stakeholders from the industrial, scientific, financial, and cultural sectors, as well as representatives from the world’s 500 largest companies, chambers of commerce, and state-owned enterprises. This gathering was an opportunity to foster collaboration and explore synergies between Changzhou and Shanghai.
A speech by Changzhou Mayor Zhou Wei highlighted the city's commitment to deepening cooperation and stimulating innovation. Our partnership with the Changzhou Xitaihu Science & Technology Industrial Zone strengthens our commitment to developing cutting-edge surface treatment technologies in the electric mobility and aeronautics sectors.
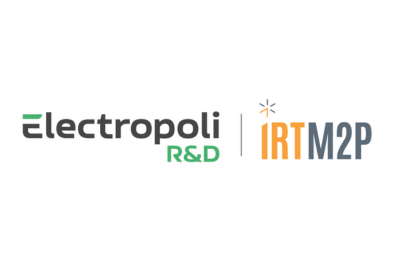
- 🔬 APOLLO Project: Towards a new generation of sustainable, high-performance industrial surface treatments
Electropoli is honored to be taking part in the APOLLO (Aluminum Protection through cOnversion without harmfuL hexavaLent chrOmium) project, a strategic initiative led by IRT M2P in collaboration with industrial partners and academics. Launched in June 2024, this project is part of a strict regulatory framework, imposed by the European REACH regulation, and aims to transform surface treatment methods for aluminum alloys in order to meet today's environmental and industrial challenges.
🎯 Objectives of the APOLLO project
The APOLLO project has two main aims:
1️⃣ Enhancing the robustness of TCP (Trivalent Chromium Process) treatments:
Improving corrosion protection performance, particularly in demanding environments such as aerospace and defense.
Optimization of surface preparation steps to ensure uniform and reproducible application of conversion layers.
2️⃣ Developing a chromium-free alternative:
Based on promising formulations, such as those based on potassium permanganate, which offer comparable performance to current CrIII- or CrVI-based treatments.
🌍 Industrial and environmental challenges
The APOLLO project is not limited to a simple technological improvement. It also aims to:
Guarantee compliance with European standards while preserving the competitiveness of manufacturers.
Protect workers' health by eliminating hazardous substances.
Reduce the overall environmental impact of surface treatment processes.
📈 Prospects and benefits
APOLLO marks a crucial step in the transition to sustainable processes. The expected results include:
Robust industrial qualification of TCP solutions.
Wider adoption of chromium-free alternatives.
Better control of processes within the supply chain.
Together, we are moving towards an industry that is more respectful of the environment and better prepared for the challenges of tomorrow.
The future of surface treatment is being built today with ELECTROPOLI and APOLLO.
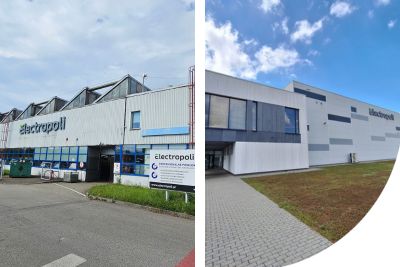
TISAX: New certification for our Polish plants
We are proud to announce that our 2 Electropoli Group Polish plants, Nowa Sol and Bielsko Biala, have recently achieved TISAX® (Trusted Information Security Assessment Exchange) certification, reinforcing our commitment to maintaining rigorous information security standards for our customers and partners. We are also TISAX®-certified in the Czech Republic and have numerous other certifications at all our plants.
What is TISAX® certification?
TISAX® certification is an international standard, designed to meet the specific needs of industries such as automotive 🚗, aerospace ✈️, and other sectors where data security is crucial.
Why is this important for the metal surface treatment industry?
Innovation relies on advanced technical processes, often developed in collaboration with customers and strategic partners. These processes include sensitive technical data, engineering specifications and optimised production methods, requiring strict management of information security.
With this certification, we are strengthening our ability to:
- Protect the confidential information of our customers and partners
- Ensure business continuity by minimising the risk of data leaks or cyber attacks
- Strengthen our position on the international market by meeting the exacting requirements of the industry's major principals.
🌐Find out more about our certifications:
https://lnkd.in/dR64GNVb
https://enx.com/tisax