Electropoli
European leader in surface treatment
We have been developing a wide range of strategic research areas for more than 70 years, which today enable us to support you in every aspect of your project.
Drawing on our extensive surface treatment expertise, we undertake to provide you with advice and deliver solutions that not only meet your specifications but also include any related requirements you may have (logistics, quality, environment, packaging, etc.)
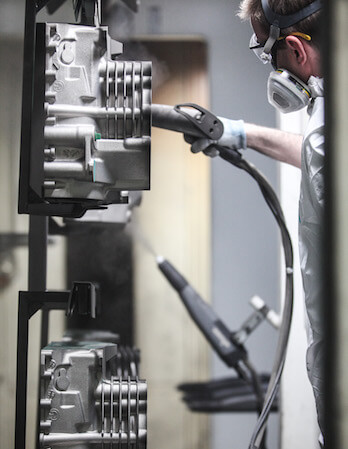
Alkaline zinc plating: anti-corrosion coating by electrodeposition
Surface treatment specialist Electropoli helps you ensure effective protection of your parts for the car, motorcycle, heavy transport vehicle, and even armaments industries by means of the alkaline zinc plating process. This surface treatment, whereby a zinc-based coating is deposited electrolytically, is exceedingly effective at preventing corrosion in steel base materials. How does alkaline electrolysis produce a zinc coating? How does it improve your parts? Electropoli explains all you need to know about alkaline zinc plating by electrolysis!
What is alkaline zinc plating?
Alkaline zinc plating, equally called cold galvanizing, electrolytic zinc coating, or electrogalvanization, uses electrolysis to deposit a layer of zinc on a steel base material in an alkaline medium, i.e., a basic (alkaline) pH aqueous solution.
Electrolytic zinc coating in an alkaline medium
The parts are first prepared (stripped down, degreased, cleaned, rinsed, etc.) then soaked in an alkaline solution containing zinc particles, ready for proceeding with electrolytic zinc coating. To do so, an electric current is applied in an alkaline bath causing the zinc particles to migrate to the cathode, which in our instance is the base metal. This technique of coating by electrolysis ensures the base metal will have good anti-corrosion properties as well as a top-grade finish.
Electrogalvanization specifics
Depending on the required result, other metals can be added to the zinc.
Furthermore, electrogalvanization is not limited to an alkaline medium. It can just as well be done in an acid medium, which also guarantees excellent anti-corrosion properties. Indeed, that’s exactly what our ZELTEC 1.1 and ZELTEC 2.4 surface treatments do!
Alkaline zinc plating properties
Whatever form the surface treatment operation takes, cold galvanizing gives the base metal great resistance to red rust. Alkaline zinc plating gives steel parts highly effective protection against corrosion, guaranteeing them a longer service life. The alkaline zinc plating treatment can also be tuned to improve the strength, toughness, and other mechanical properties of the base metal.
Last but not least, with electrolytic zinc coating, you can always achieve a great finish. The parts thus treated have a wonderfully uniform appearance. You can even obtain various coloured finishes on the parts: shades of grey, black, etc.
Bespoke surface treatment by electrogalvanization
Do you want to cold galvanize your metal parts for the automotive, armaments, aerospace, or other sectors? Alkaline zinc plating specialist Electropoli provides you with all types of surface treatment. In order to ensure a good fit with your market and to best match your needs, we can carry out these surface treatments in any of our French, Polish, or Czech factories. Transport logistics, preparation, treatment, delivery, etc. We are able to set up ideal protocols with you to assist you in your business and take the weight off your mind.
Discover our alkaline zinc plating treatments
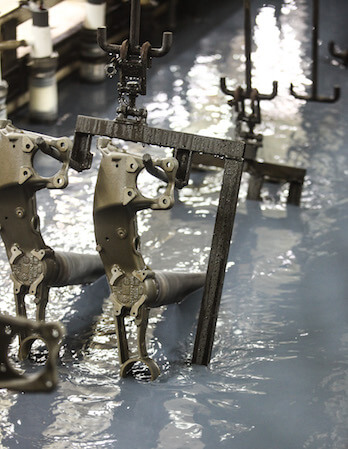
Cataphoresis treatment to effectively prevent corrosion
Cataphoresis treatment prevents corrosion of industrial metal parts. What is cataphoresis treatment? What are the benefits for industrial parts made withdifferent metal substrates? Electropoli, a specialist in surface treatments, will explain everything!
Cataphoresis treatment: what is it?
Cataphoresis, also called electrophoresis deposition(cationic electrophoresis), is a surface treatment that consists of electrochemically depositing an epoxy-type coating on a metal part (steel, cast iron, aluminium, magnesium, etc.) This industrial painting technique is widely used in the automotive industry as well as industires involving heavy-duty machinery, motorcycles, aircrafts, energy, and weapons. This anti-corrosion treatment is also one of the most suitable for steel, aluminium, magnesium, or cast/wrought iron products.
The speration of ions during electrophoresis allows the cataphoresis paint to be uniformly deposited over the entire surface of the part, which fully protects it from corrosion.
To carry out a cataphoresis treatment, the part is immersed in a water-soluble paint bath where it isispolarised (by a cathode) via an electric current. This allows the paint particules that are suspended in the bath to migrateand deposit on the part. This process guarantees that the cataphoresis paint is uniformly deposited on almost the entirety of the submerged part.
Preparation of the part for cataphoresis treatment
The preparation of a part before cataphoresis painting is as important as the treatment itself. Depending on the base material, the parts may undergo severalstages of preparation (degreasing, rinsing, stripping, phosphating, etc.) before the paint is actually deposited. Once this step has been completed, the parts can go through the paint bath and receive the cationic electroplating. At the end of the process, the parts are rinsed again, then firedgenerally between 180 and 200°C topolymerise and fix the deposit.. Thislaststep createsan inert organic layeron the part. The chemical passivity of this layer makesthe partresistant to corrosion.
Advantages of cataphoresis treatment
Cataphoresis painting first and foremost protects the parts against corrosion, but there are also other advantages to this treatment:
- - The the entire surface of the treated parts are protected: hollow areas, concealed areas, sharp edges, etc.
- - The treatment, a 10-40 micrometer layer of paint, is applied evenly over the entire part.
- - The black cataphoresis paint also has aesthetic benefits, as it gives the part a beautiful uniform glossy appearance.
- - It is an eco-friendly treatment, since it requires the use of very few chemicals.
Are you convinced of the benefits of cataphoresis treatment? You want to guarantee that your parts are effectively protected against corrosion. Parts made of steel, cast iron, aluminium, magnesium, etc. Electropoli has cataphoresis treatment service centres located in Saumur (Fr), Nowa Sól or Bielsko-Biala (Pl) and Tremosnice (Cz).
Electropoli also provides you with other surface treatment services, including electrolytic treatments, chemical treatments andhot-dip galivanising.Regardless of the industry - automotives, motorcycles, HGVs, aeronautics, weaponry, etc. - we can set up customised surface treatment processes for all your parts.Contact us now!